Category
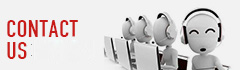
Contact person: Zhang Xingqian 13912340688
Phone: 0519-81182602
Fax: 0519-81182602
whatsapp:+8618961131360
Website: www.yzdryer.com
Email: yz@yzdryer.com steven@yzdryer.com
HZG series rotary drum dryer
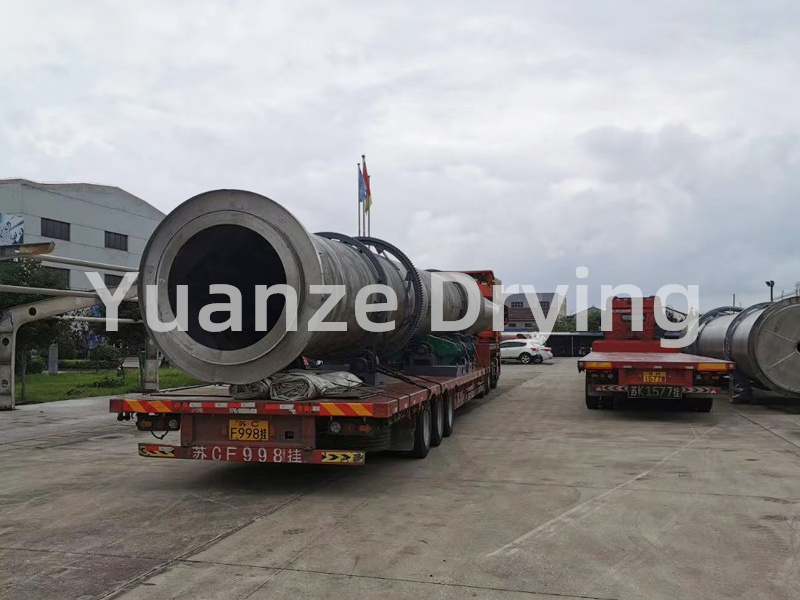


HZG series rotary drum dryer
Description
After the wet material is inserted from one end of the dryer, under the flipping of the inner uniformly distributed plate reader, the material is evenly distributed and dispersed in the dryer, and fully contacts with the co current (counter current) hot air, accelerating the drying flow and mass transfer driving force. During the drying process, the material can be adjusted to move to the star shaped discharge valve at the other end of the dryer under the action of a tilted plate and hot air flow
1. In industries such as chemical, mining, and metallurgy, large particles and materials with high density are dried, such as ore, blast furnace slag, coal, metal powder, phosphate fertilizer, and ammonium sulfate.
2. Drying of powdered and granular materials with special requirements, such as HP foaming agent, distiller's grains residue, lightweight calcium carbonate, activated clay, magnetic powder, graphite, and pharmaceutical residue.
3. Materials that require low-temperature drying and require continuous drying in large quantities.
1. The rotary dryer has a high degree of mechanization and a large production capacity.
2. The fluid has low resistance through the cylinder and low functional consumption.
3. Strong adaptability to material characteristics.
4. Stable operation, low operating costs, and good uniformity of product drying.
model | Direct heating downstream type | Direct heating downstream type | Direct heating downstream type | Direct heating downstream type | Composite heating | Composite heating |
Material type | ore | HP foaming agent | blast furnace slag | ammonium sulfate | phosphate fertilizer | coal |
Processing capacity (kg/h) | 1000 | 466 | 15000 | 20000 | 12000 | 5000 |
Discharge water content (%) | 30 | 13 | 6 | 1.5 | 5 | 6.5 |
Final moisture content (%) | 15 | 0.3 | 1 | 0.1 | 0.1 | 0.1 |
Average particle size (mm) | 6.5 | 0.05 | 4.7 | 0.5-1.7 | 0.5 | 5 |
Material stacking density (kg/m3) | 770 | 800 | 1890 | 1100 | 1500 | 750 |
Hot air volume (kg/h) | 3900 | 5400 | 10750 | 9800 | 6500 | 16000 |
Inlet gas temperature (oC) | 600 | 165 | 500 | 180 | 650 | 570 |
Material outlet temperature (oC) | 42 | 100 | 70 | 80 | 75 | |
Heating method | coal gas | Steam electric heating | heavy oil | JRF | heavy oil | heavy oil |
loading coefficient | 6.3 | 7 | 7.5 | 7.8 | 18 | |
speed(rpm) | 4 | 4 | 3.5 | 3 | 4 | 2 |
inclination | 0.04 | 0.005 | 0.03 | 0.05 | 0.05 | 0.043 |
Number of copied boards | 12 | 24 | 12 | 22 | Outside the inner cylinder 8 Outside the inner cylinder 16 | 6 12 |
Drier diameter (m) | 2.0 | 1.5 | 2 | 2.3 | outer cylinder 2 inner cylinder 0.84 | outer cylinder 2.4 inner cylinder 0.95 |
Dryer length (m) | 20 | 12 | 17 | 15 | 10 | 16 |
Drive power (kw) | 22 | 7.5 | 15 | 11 | 11 | 15 |